What is a stepper motor ?
What is a stepper motor ?
A stepper motor is one that rotates in an intermittent manner, moving by a fixed angle at each step rather than continuously rotating its shaft.
The movement of the second hand on a clock, for example, which advances one second at a time, could be achieved by using a stepper motor that moves in 6°increments, once every second.
So, how does a stepper motor achieve this characteristic of rotating its shaft by a fixed angle at each step?
The secret lies in the use of electrical pulses. A pulse is an electrical signal produced by turning a power supply on and off, with each such switching counting as one pulse. A stepper motor uses these pulses to achieve precise mechanical control over the angle and speed of rotation.
Stepper motors can be broadly grouped into the following three categories depending on the structure of their rotor.
Permanent magnet (PM) motor:
The rotor contains a permanent magnet. A disadvantage of this structure is that it can not provide flexibility over the angle of rotation (step angle).
Variable reluctance (VR) motor:
The rotor contains cores structured like the teeth of a gear. This allows for more flexibility in setting the step angle.
Hybrid (HB) motor:
The rotor contains both permanent magnets and cores structured like the teeth of a gear. This type of motor is used in a wide variety of applications, combining the advantages of PM and VR motors.
Operation principle of HB stepper motors:
The rotor is designed with a cylindrical permanent magnet positioned between two cores, these being concentric to the motor shaft and offset by a half pitch from each other. The rotor rotates by a fixed step angle each time a pulse is input.
Stepper motors can also be grouped into the following two categories based on electric current flow in the coil:
Unipolar motor:
Current in a unipolar motor always flow through the coil windings in the same direction. While this keeps the associated control circuit simple, it produces less torque than a bipolar motor.
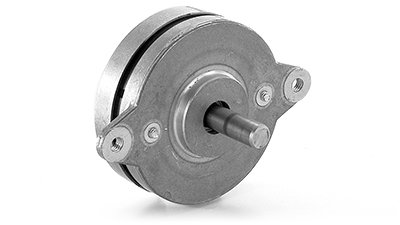
Bipolar motor:
Current in a bipolar motor can flow through the coil windings in either direction. While this requires a more complex control circuit than a unipolar motor, it produces more torque.
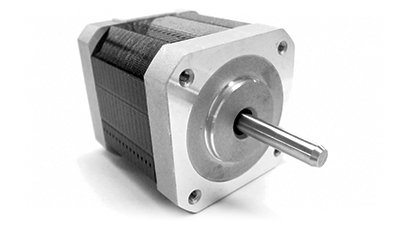
What is a stepper motor driver?
Stepper motors are used in conjunction with a driver circuit. The driver controls the angle and speed of motor rotation based on the input of electrical pulses from the controller.
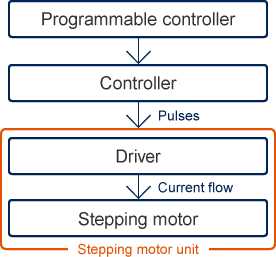
Features of stepper motors:
Stepper motors differ from other motor types in the following ways.
Advantages:
- As the angle of rotation is determined by the number of pulses (digital input), control of position (angle of rotation) is simple
- Can rotate at low speeds
- Can use open-loop (non-feedback) position control
- Excellent ability to remain locked in position when halted
Disadvantages:
- Requires a drive circuit
- Loss of synchronization can occur due to factors such as unexpected changes in load
- High level of vibration and noise
Applications for stepper motors:
The excellent halting accuracy, high torque at medium and low speeds, and superior responsiveness of stepper motors means that they can be used in a wide range of drive applications that demand precise control.
- Production machinery
- Medical equipment
- Laboratory analytical instruments
- ATMs
- Vending machines
- Ticket vending machines
- Copiers
- Robots
- Optical disk drives (Blu-ray and DVD drives, etc.)
- Laser printers
- Digital cameras
- Air conditioning louvers
- Amusement machines
Santiago Martinez – www.windydaysproducts.com